Elektrifiering av nya bilar bidrar till minskade utsläpp, men samtidigt till ökad vikt. Därför är det stort fokus på viktbesparande åtgärder i nybilteknik. Nissan har utvecklat nya lösningar som minskar utvecklingstiden och bidrar till säkrare, mer bränsleeffektiva och helt enkelt roligare bilar att köra.
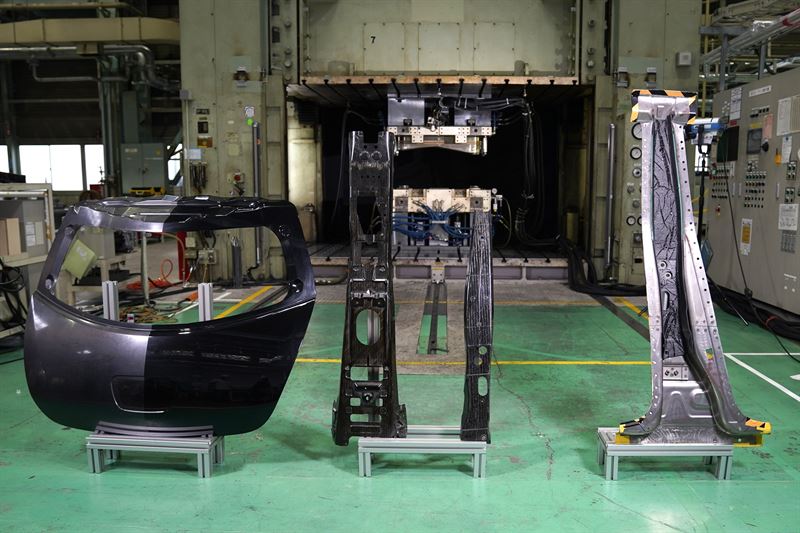
Kolfiberförstärkt plast (CFRP) ett material som används i flygplan, raketer och sportbilar kan komma att användas i massproduktion av bilar tack vare en ny produktionsprocess som Nissan har utvecklat.
Det exklusiva lätta materialet har vanligtvis ett högt pris men är eftertraktat på grund av fördelarna, samt att det har cirka 50 % lägre vikt än stål. Tack vare en ny produktionsprocess som utvecklats av Nissan kan detta material snart gå i massproduktion på nya bilar.
Den nya processen påskyndar utvecklingen av bildelar tillverkade av kolfiber och förstärkt plast (CFRP). Detta material har sina stora styrkor genom att det är mycket lätt men samtidigt mycket starkt och vridstabilt. Materialet är därför utmärkt för att göra nya bilar säkrare och mer bränsleeffektiva. Det ger också möjlighet att sänka tyngdpunkten, vilket i sin tur bidrar till bättre köregenskaper.
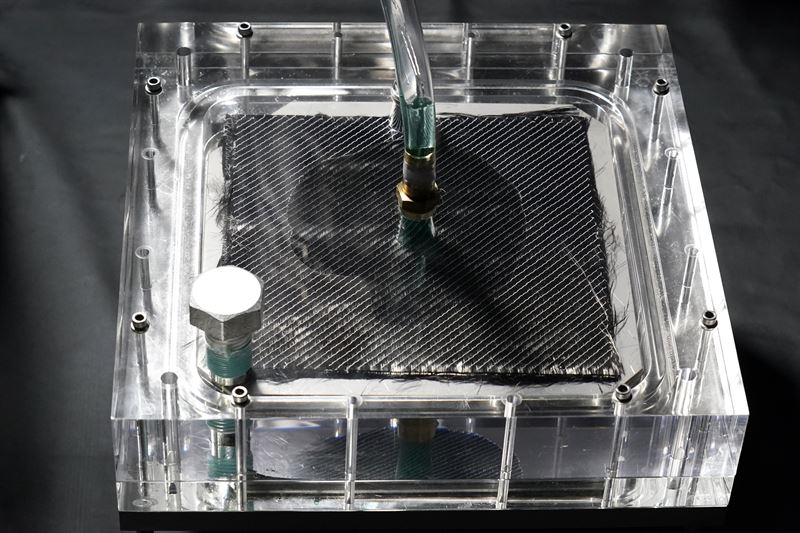
Nissans mål är att kunna tillämpa den nyutvecklade processen för massproduktion av CFRP-delar och introducera dem i flera kommande bilmodeller. Innovationen kan minska produktionstiden avsevärt jämfört med traditionella metoder.
Fördelarna med detta material har varit kända under lång tid, men utmaningen har också varit de höga kostnaderna jämfört med stål. Dessutom har det inte varit särskilt lämpligt att massproducera bilar med detta material, eftersom det har varit komplicerat att forma CFRP-delar.
Nissan har hittat ett nytt alternativ till den befintliga produktionsmetoden. Metoden förkortar formens faktiska utvecklingstid med 50 % och gjutningsprocessen med så mycket som 80 %. Detta ger stora besparingar och därmed möjligheter att kunna använda materialet vid massproduktion av framtida bilar, med alla fördelar det ger.